On November 14th 2024, the Landschaftsverband Westfalen-Lippe (LWL) at Münster presented a tiny golden lock from around the year 400 (1600 years ago). This news was published on the 28th of January by the LWL, and widely shared. Most articles written on the topic used the smallest version of the photos they could find, and glanced over the details. We chose to write this article after re-discovering the original article and studying the inner workings of the lock.
Feel free to check out the original article, first. The article has loads more details on the history, as well as videos of the CT scan and the working principle of the 4x model: https://www.lwl.org/pressemitteilungen/nr_mitteilung.php?urlID=60628
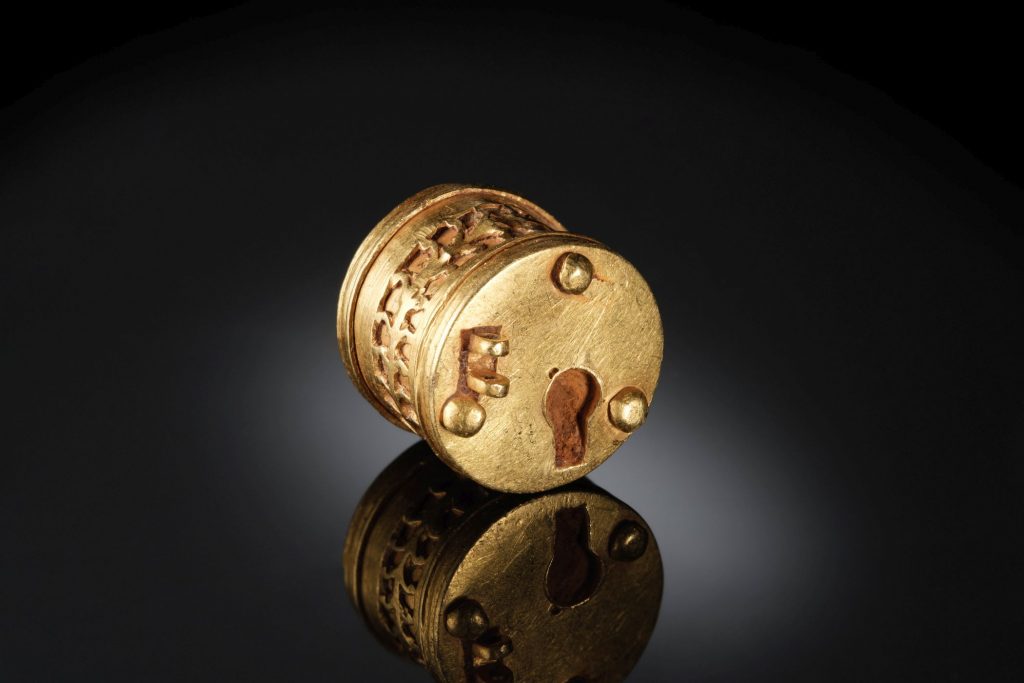
While it doesn’t look too special at first glance, this lock is s quite an engineering marvel. At just 11 mm high with a diameter of 12 mm, it’s tiny. The engineering is quite similar to engineering in horology and takes incredible skill to make something like this today, let alone with the tools from 1600 years ago.
The lock looks great from the outside, but to really, appreciate the complexity. We will have to look at the Neutron tomography CT-scan the researchers created. The images may not look like much to the untrained eye, but the researchers published the post-processed images to show the specific parts.
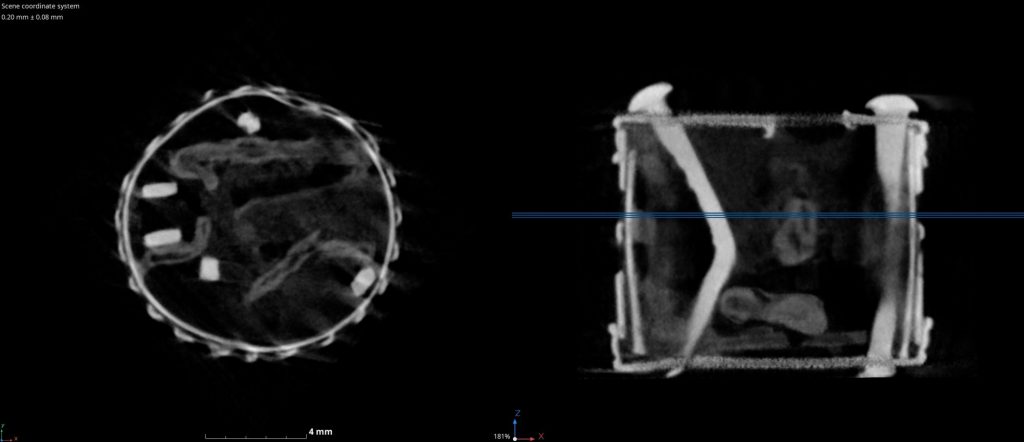
Photo copyright: Paul-Scherrer-Institut/Villigen [CH]/ David Mannes
The next image is the processed CT-scan where specific parts are colored. The article gives the following explanation: frame with spring (red), bolt (blue), broken bolt (?) (yellow), piece of the key (green), baseplate (purple) and inserted chain link (orange). The original article provides a video of the CT-scan as well. The video is in the attachments to the original article, with the name: “Anlage 1: Dosenschloss_Neutronen_CT_Animation.avi”.
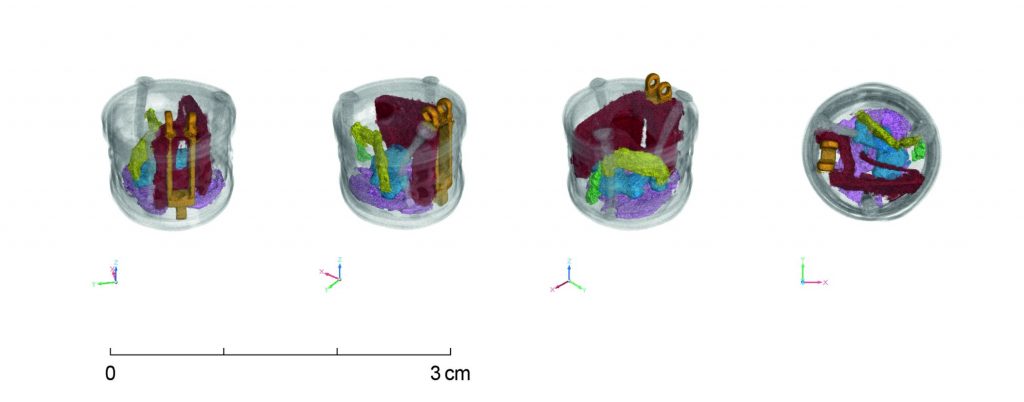
Photo copyright: Paul-Scherrer-Institut/Villigen (Schweiz)/David Mannes; Montage: LWL/Corinna Hildebrand
With the information from the CT-scan, Stefan Brentführer set out to make a functioning replica. He chose to make the replica larger, likely to better show how the lock works, as well as it is easier to work on larger parts. This exploded view is quite well done, but it doesn’t show clearly how the parts fit together. If you are up to the task, take a moment to puzzle to see how these pieces fit together.
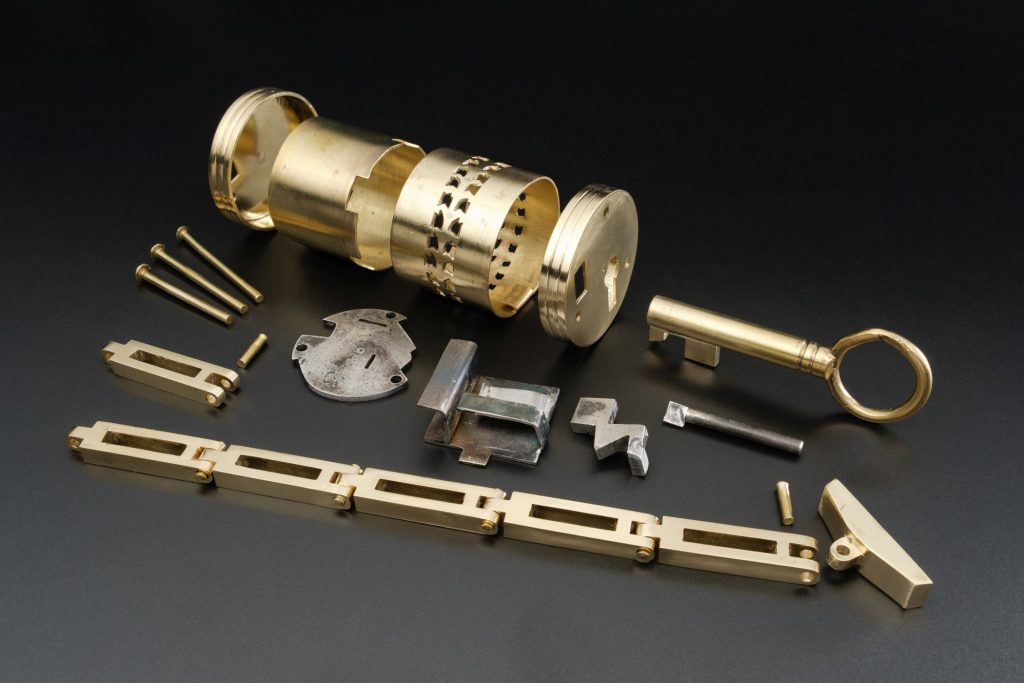
Photo copyright: LWL /Stefan Brentführer
While locks which require a rotational motion to open can only be opened in either clockwise or counter-clockwise rotation, this lock operates clockwise, as do most locks in use today. Does someone know examples of counter-clockwise operating locks from 1600 years ago?
I’ve puzzled that the steel piece in the middle fits upright and horizontal on the round backplate. It has a matching piece which fits the rectangle hole. This leaves a square opening for the square linkage. The second diagonal rectangle hole is for the round post. (Yes, this tiny lock has a pipe key!) The cutout on the key corresponds to the bridge on the middle plate. From there it got confusing, and where I got some help. The bolt fits under the bridge into a barely visible rectangle hole to the top left next to the spring.
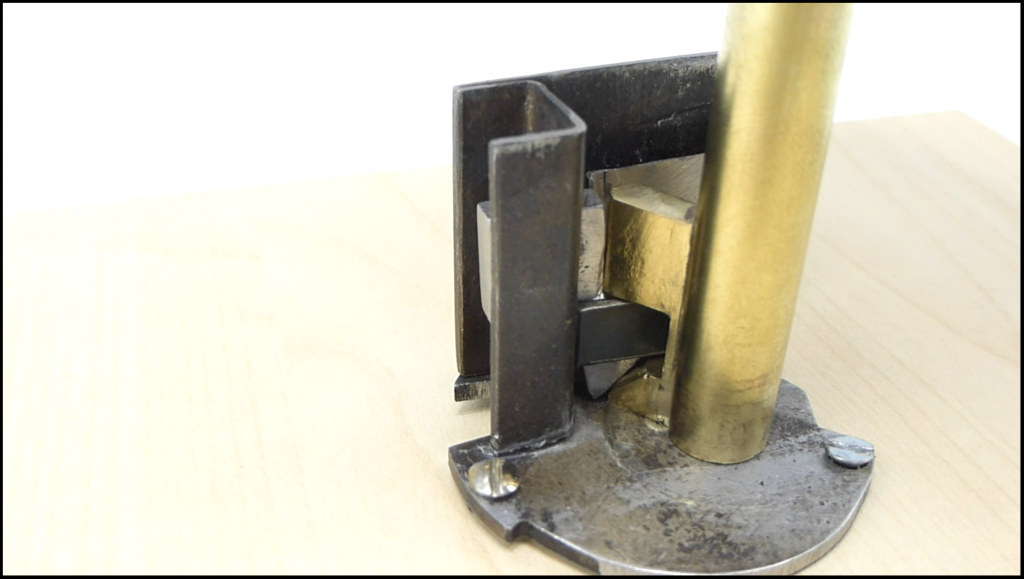
Photo copyright: LWL /Stefan Brentführer
The lock’s operating is rather clever as it reuses the spring to keep the bolt in place in either positions. With the bolt closed and the key rotating in the clockwise direction, the fat bit of the key pushing down the spring that traps the bolt in the locked position. The triangle tip of the key perfectly fits the triangle cutout on the bolt. The bolt is moved on top of the spring, while the key holds the spring down. The closing operation is identical, but in reverse. Stefan Brentführer made a video of the operation and added it to the original article under “Anlage 2: Dosenschloss_Rekonstruktion_Schliessvorgang.MP4”.
Toool didn’t have a role in the research, but we believe these moments should be chearished and the news shared widely. My contribution, beside this blog, was the work to demonstrate how small the lock really is. I’ve made a mock-up of the lock in OpenSCAD and printed a copy with an FFF 3D printer. The files are attached, in case you are curious or want to print your own.
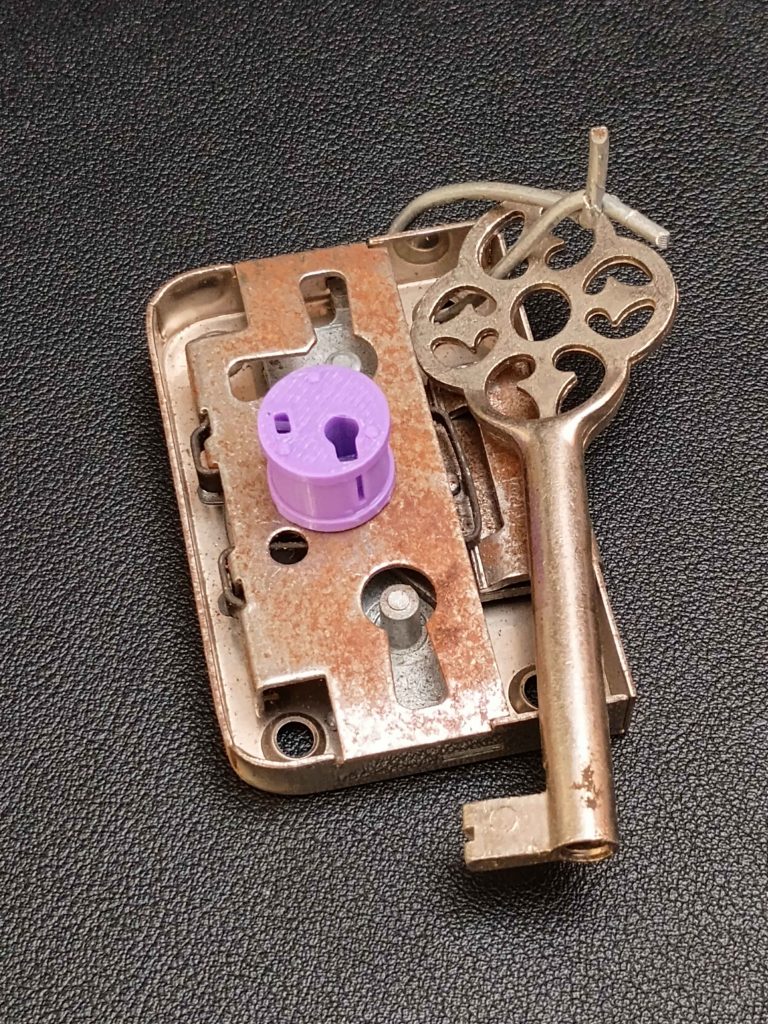
Nigel from Toool UK went a different route, and chose to model the mechanism in a 3D CAD program, with great result!
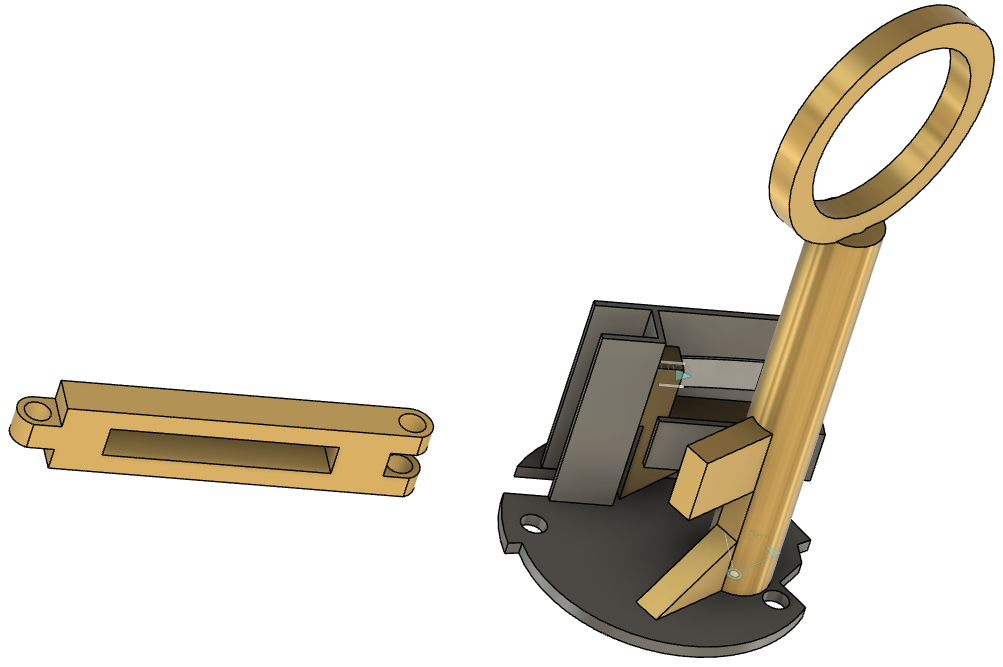
The photos in this post are mostly from LWL /S. Brentführer. They kindly give permission to share the pictures in the context of the finding. The article is the creative work of Jan-Willem Markus. This text is copyright CCBY4.0 Toool Blackbag.